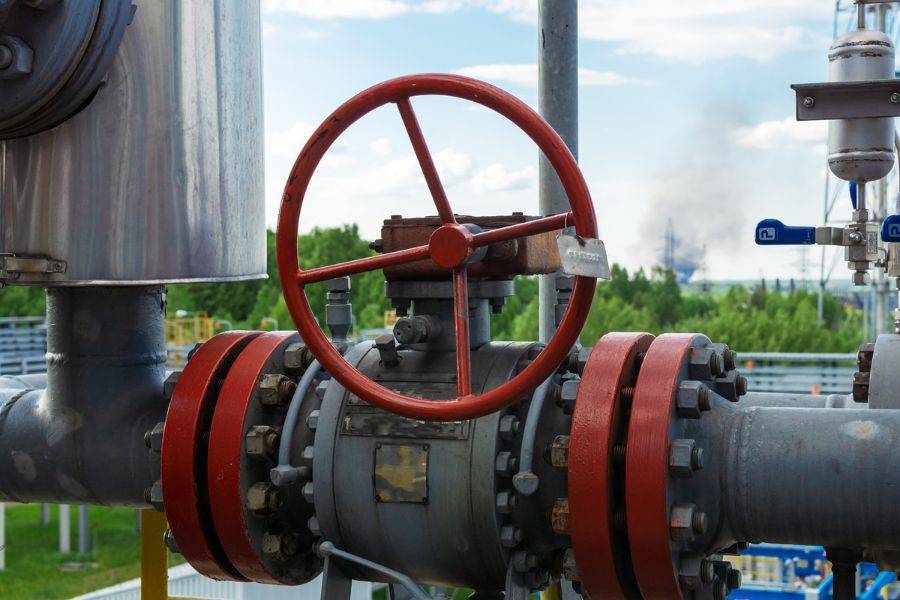
Does a Slurry Valve Impact the Efficiency of Your Slurry Pump?
Slurries are a problematic fluid to pump. They can be abrasive or corrosive and usually contain a high percentage of solids, which makes them thick and dense. This is tough on process equipment, causing wear and tear over time. Choosing the right slurry pump is important, but so is choosing the right slurry valve.
How to choose the correct slurry valve for your pump?
To understand what slurry valve to choose, you need to know the percentage of solids your pump will deal with. Slurries usually contain 30-60% solid material, and some can contain percentages as high as 60-70%. Understanding this ratio ensures that you select the right valve material and size. Large slurry particles can block a valve with narrow restrictions. To prevent jamming, make sure that the slurry valve is suited for your process conditions. Once you have identified particle size and process conditions, you can look at the following factors before choosing the correct slurry valve:
- Material compatibility: Most standard valves won’t hold up against slurries, especially abrasive or corrosive ones. Ensure the valve material is compatible with the slurry’s abrasive properties or chemical composition. Friction can also affect your decision, as it stresses the valve components. Valve gates and seats should comprise materials that can withstand harsh process conditions. Consider rubber-lined valves for corrosive slurries and hardened materials like stainless steel for abrasive ones.
- Flow rate: Flow rate is crucial, impacting wear and material loss. It’s important to match the valve type and size to the intended flow.
- Pressure and temperature: Evaluate the slurry’s maximum temperature and pressure, especially when choosing materials for valve sleeves or seats. Different elastomers and polymers are suitable for varying temperature ranges. Elastomers and polymers with good wear characteristics usually service temperature of up to 120 degrees. Certain valves, such as ball, butterfly, and pinch valves, can also offer varying degrees of control. For example, diaphragm or pinch valves are typically used for low-temperature and low-pressure slurries. The valves become more specialized for heavy-duty slurries operating under high temperatures and pressure.
- Maintenance and reliability: Valves in slurry applications often face significant wear and tear. Opt for valves with robust construction and easy maintenance features to minimize downtime and ensure long-lasting operation. You can also look for valves with good sealing capabilities to prevent leakage.
- Scaling Potential: Viscous and abrasive media can cause scaling or crystallization, so it’s essential to understand the risk to your equipment’s lifespan and even your production targets. Fortunately, valve components, including the seat, coating, and actuator control schemes, can be designed to manage and prevent scale build-up within the valve.
Slurry valves can have a significant impact on your operation. Make sure to consult with a qualified engineer when you analyze slurry characteristics and your desired performance. The cost of premature valve failure is far greater than the effort to choose the correct slurry valve for your pump.
If you’re in doubt or simply want some expert tips and advice, call us at 1-800-367-4180 (toll-free). As your industrial pump supplier in Canada, we’re here to help you choose, install, maintain, and monitor a variety of equipment. And to answer questions about things you’ve previously tried gone wrong.