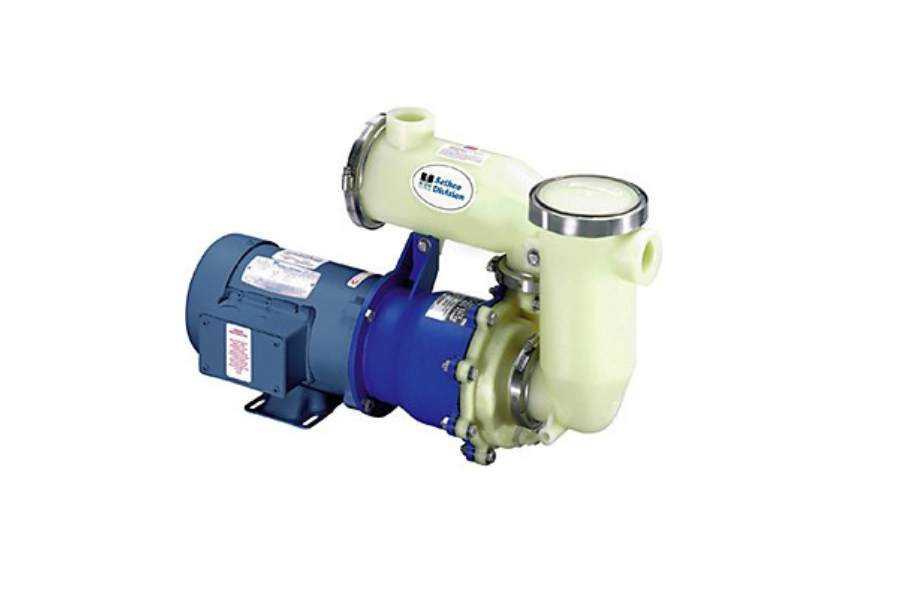
Why Use Magnetic Drive Pumps in Industrial Applications?
In today’s industrial landscape, efficiency and safety are paramount concerns for operations managers and engineers alike. Traditional sealed pumps often present challenges with leakage and maintenance when handling corrosive, toxic, or valuable fluids. Magnetic drive pumps offer an innovative solution to these problems, providing leak-free operation and enhanced reliability for critical applications.
What Are Magnetic Drive Pumps and How Do They Work?
Mag drive pumps utilize magnetic coupling instead of traditional mechanical seals to transfer power from the motor to the impeller. This design features two magnets—one connected to the motor shaft and another attached to the impeller. When the motor runs, the outer magnet drives the inner magnet through magnetic force, eliminating the need for a direct mechanical connection and creating a wholly sealed pumping chamber.
Key Benefits: Leak-Free, Low Maintenance, and High Efficiency
The sealless design of mag drive centrifugal pumps provides several significant advantages:
- Zero Leakage: Without mechanical seals that can wear and fail, these pumps eliminate the risk of fluid leaks—critical when handling hazardous chemicals.
- Reduced Maintenance: Fewer moving parts mean less wear and tear, resulting in lower maintenance costs and less downtime.
- Environmental Compliance: The leak-free operation helps facilities meet strict environmental regulations and avoid costly cleanup procedures.
- Extended Lifespan: Without seal friction and wear, these pumps often outlast their traditional counterparts in demanding applications.
Industries That Benefit from Mag Drive Centrifugal Pumps
Several sectors find particular value in magnetic drive pump technology:
- Chemical Processing: For handling corrosive and toxic substances safely
- Pharmaceutical Manufacturing: Where product purity and contamination prevention are critical
- Semiconductor Production: For ultra-pure water and chemical transfer applications
- Food and Beverage: Where sanitation and contamination prevention are essential
- Wastewater Treatment: For reliable handling of corrosive treatment chemicals
How to Choose the Right Mag Drive Pump for Your Needs
When selecting a mag drive pump for your application, consider these factors:
- Fluid Properties: Viscosity, temperature, and corrosiveness
- Flow Rate Requirements: Ensure the pump can handle your required capacity
- System Pressure: Match the pump’s capabilities to your system’s demands
- Material Compatibility: Choose construction materials that resist corrosion from your specific fluids
- Power Source Availability: Electric or alternative power options
Best Practices for Maintenance and Longevity
Though magnetic drive pumps require less maintenance than sealed alternatives, proper care ensures optimal performance:
- Monitor fluid temperature to prevent overheating
- Ensure adequate NPSH (Net Positive Suction Head) to prevent cavitation
- Install appropriate filtration to keep abrasive particles from damaging the pump
- Perform regular inspections of bearings and magnetic coupling
- Follow the manufacturer’s guidelines for recommended maintenance intervals
A Worthwhile Investment
Investing in mag drive pumps provides immediate and long-term benefits for industrial operations. The elimination of leaks, reduced maintenance requirements, and enhanced safety features make these pumps an excellent choice for facilities handling dangerous, valuable, or sensitive fluids. By selecting the right magnetic drive pump for your specific application, you can ensure safer operations, reduced environmental risk, and improved overall efficiency for years to come.