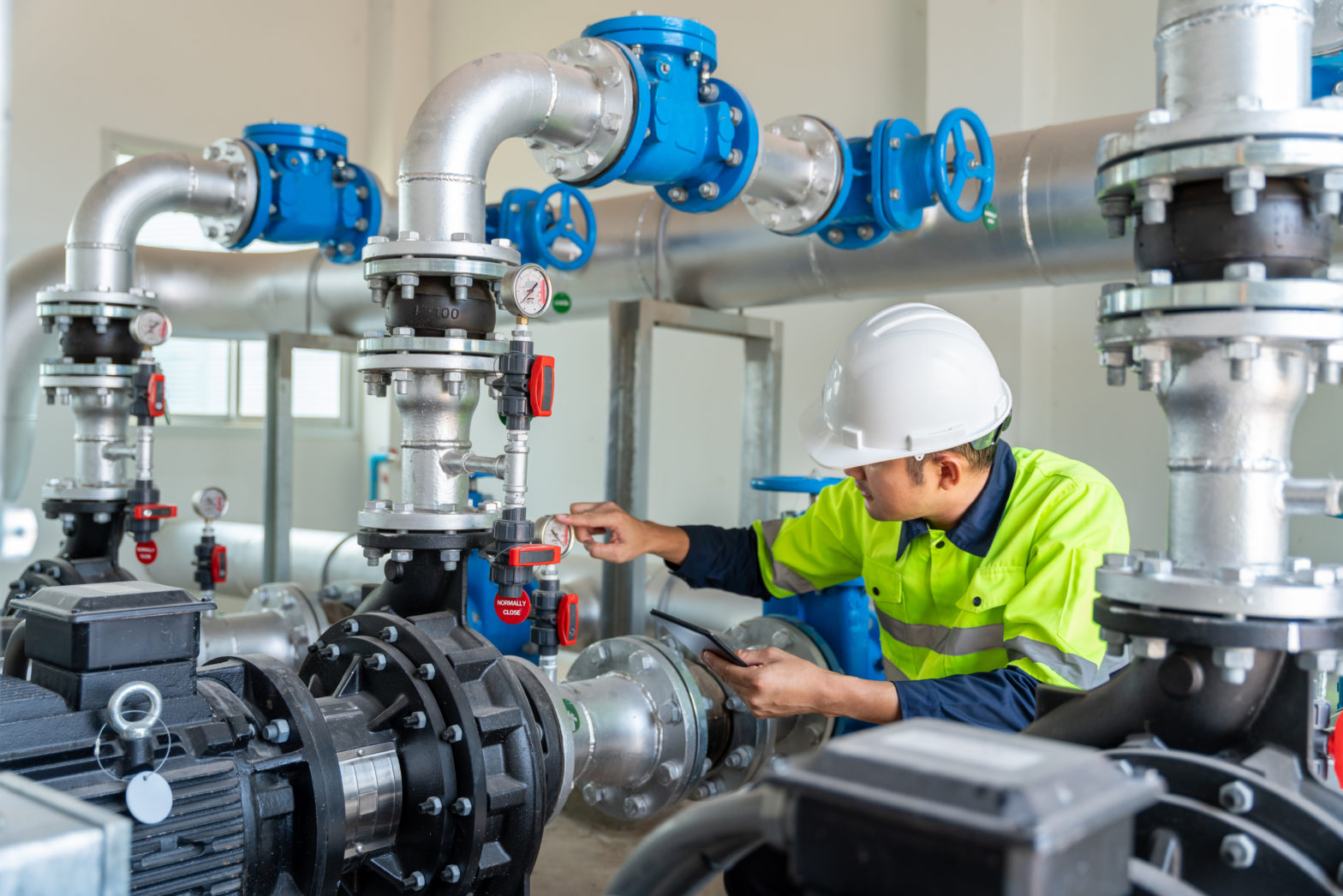
The Value of Integrating Modern Pump Technologies into Traditional Industries
In traditional industries like manufacturing, agriculture, and water treatment, pumps have literally been a long-term fixture and an essential part of operations. As technology evolves, so do the tools and systems that drive these industries. Pump technologies have come a long way. We’re now in the age of IoT (Internet of Things) and predictive maintenance, which are transforming how industries manage their operations.
It’s important to remember that new technologies can enhance efficiency, reduce downtime, and significantly improve overall performance in legacy industrial settings. This will lead to more efficient, reliable, and cost-effective operations, ultimately providing businesses with a competitive edge.
The Role of IoT in Modern Pump Systems
The Internet of Things (IoT) has been simplified over the decades to a point where it can currently change the way industrial equipment is monitored and controlled. For pump systems, IoT enables the real-time monitoring of critical performance metrics like your flow rate, pressure, temperature, and energy consumption. Sensors installed in pumps will gather this data and send it to centralized control systems or cloud platforms, where operators can analyze trends and find potential issues before they lead to system failures.
Benefits of IoT-Enabled Pumps
- Real-Time Monitoring: IoT integration allows operators to monitor pumps remotely, offering real-time visibility into the system’s performance. This level of insight helps identify problems like declining efficiency or wear and tear on components.
- Predictive Maintenance: Instead of relying on scheduled maintenance or waiting for breakdowns, IoT sensors can detect early signs of trouble and notify operators when parts are starting to fail. This predictive approach allows for repairs or replacements before a breakdown happens, minimizing downtime and avoiding expensive repairs.
- Energy Efficiency: By monitoring pump energy consumption in real-time, IoT systems can help optimize energy usage. Operators can adjust pump settings to ensure they are running at the most efficient levels, which leads to significant energy savings over time.
Greg Vissers, President at Vissers Sales Corp. notes, “With IoT-enabled pumps, businesses are no longer flying blind when it comes to pump performance. The ability to track every detail of how the pump is functioning means fewer surprises and more control over operational efficiency.”
Predictive Maintenance: A Game Changer for Traditional Industries
One of the key benefits of modern pump technology is the integration of predictive maintenance strategies. Traditional industries have long relied on preventive maintenance, which involves performing maintenance at scheduled intervals, regardless of whether it is actually needed. While this approach reduces the risk of unexpected breakdowns, it can also lead to unnecessary maintenance, which adds to operational costs.
Predictive maintenance, powered by IoT and advanced analytics, changes the game. By collecting and analyzing data from the pumps, businesses can accurately predict when a component is likely to fail. This allows for just-in-time maintenance that keeps equipment running at peak performance without the risk of expensive, unplanned downtime.
Key Benefits of Predictive Maintenance in Pumps
- Reduced Downtime: Predictive maintenance minimizes unplanned downtime by addressing issues before they cause breakdowns. This ensures that pump systems run smoothly and consistently, which is particularly important in industries where uptime is critical to profitability.
- Cost Savings: By only performing maintenance when necessary, businesses can reduce maintenance costs. There’s no need to replace parts that are still functioning well, and fewer emergency repairs are needed.
- Extended Equipment Life: Pumps that are maintained based on actual performance data tend to have a longer lifespan. Predictive maintenance helps avoid damage caused by running a failing component to the point of failure, which can lead to more extensive damage.
At Vissers Sales Corp., we encourage businesses to embrace these predictive technologies as part of a broader strategy to modernize pump systems.
The Future of Industrial Pumps
As traditional industries evolve, the integration of modern pump technologies is becoming essential for maintaining competitiveness and efficiency. IoT-enabled monitoring and predictive maintenance represent two of the most significant advancements in pump technology, offering businesses the tools they need to optimize operations, reduce costs, and extend the life of their equipment.
Whether you’re looking to upgrade your existing equipment or install new, cutting-edge pumps, our team at Vissers Sales Corp. can provide the expertise and support you need. Contact us today via our website or toll-free on 1-800-367-4180 to learn more about how modern pump technologies can transform your industrial operations.