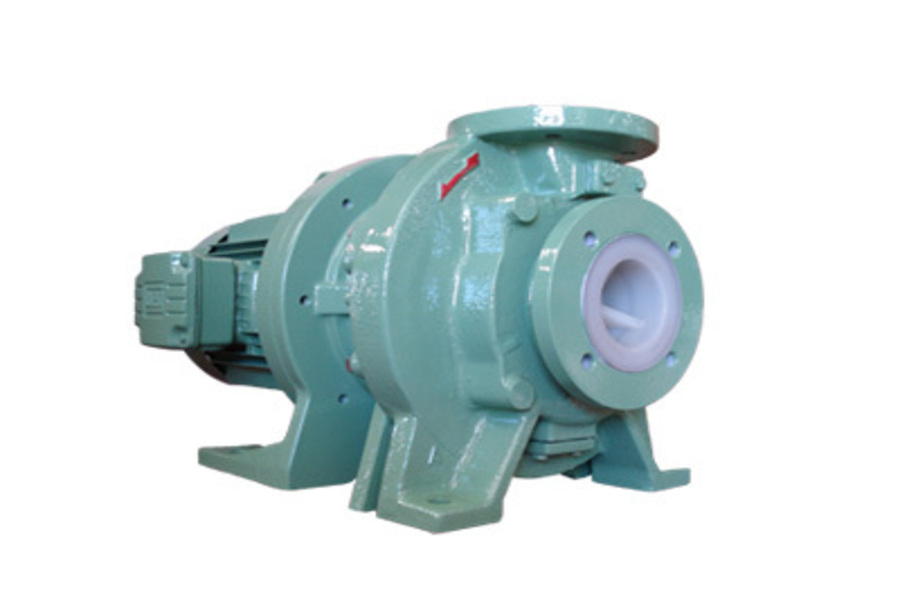
The Importance of Material Selection in Mag Drive Pumps for Corrosive Fluids
Handling corrosive fluids requires precision and reliability, making magnetic drive pumps an essential solution for industries dealing with hazardous chemicals. Unlike traditional pumps, which use seals, mag drive pumps feature a sealless design that reduces leakage risks and lowers maintenance costs. Selecting the right materials is crucial to ensuring optimal performance, longevity, and safety.
Understanding Corrosive Fluids
Corrosive fluids, including acids, alkalis, and solvents, can degrade pump components over time, leading to costly repairs and potential system failures. These fluids vary in concentration, temperature, and exposure duration. Understanding the chemical properties of the fluid being handled is vital for selecting the right materials for a mag drive pump, preventing deterioration, and ensuring operational efficiency.
Key Materials Used in Mag Drive Pumps
Selecting appropriate materials for a mag drive centrifugal pump is crucial for ensuring durability and efficiency. Commonly used materials include:
- Polypropylene (PP): Lightweight, cost-effective, and suitable for mild corrosive applications.
- Polyvinylidene Fluoride (PVDF): Excellent resistance to aggressive chemicals and high temperatures.
- Stainless Steel: Strong mechanical properties with broad chemical resistance.
- ETFE (Ethylene Tetrafluoroethylene): Offers superior resistance to strong acids and bases, making it ideal for harsh industrial applications.
Factors to Consider When Choosing Materials
Several factors influence material selection for a magnetic drive pump, ensuring compatibility and longevity:
- Chemical Compatibility: The material must withstand the specific chemical composition of the fluid.
- Operating Temperature: High temperatures demand materials with enhanced thermal stability.
- Pressure Requirements: Materials should endure operational pressures without deformation.
- Abrasive Properties: Fluids containing particulates require robust materials to resist wear.
Consequences of Incorrect Material Selection
Using unsuitable materials for a mag drive centrifugal pump can cause to several challenges, such as:
- Premature Failure: Increased wear and tear resulting in frequent replacements.
- Leakage Risks: Component degradation can lead to environmental hazards and safety concerns.
- Higher Maintenance Costs: Frequent servicing and part replacements raise operational expenses.
- Reduced Efficiency: Deterioration can compromise pump performance, affecting flow rates and pressure levels.
Best Practices for Material Selection
To optimize the performance and longevity of mag drive pumps, consider the following best practices:
- Consult Compatibility Charts: Utilize chemical resistance guides to ensure material-fluid compatibility.
- Field Testing: Conduct trials to verify material effectiveness under actual operating conditions.
- Partner with Trusted Suppliers: Work with reputable manufacturers to source high-quality materials.
- Routine Monitoring: Regular inspections help identify early signs of material wear and prevent failures.
Selecting the right materials for a mag drive pump ensures durability, safety, and efficiency in handling corrosive fluids. By thoroughly evaluating fluid properties and material compatibility, businesses can enhance performance, minimize maintenance costs, and provide seamless operations.